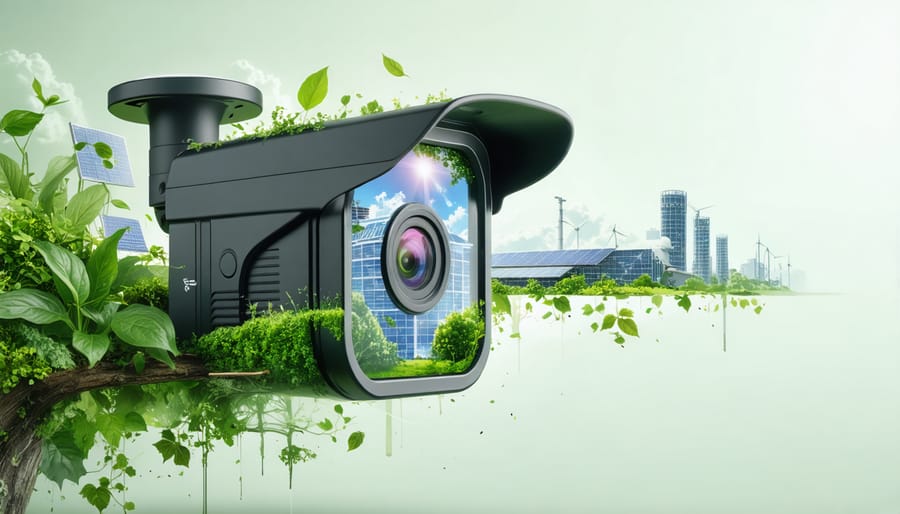
High-speed camera manufacturers are revolutionizing sustainable imaging technology while pushing the boundaries of ultra-slow-motion capabilities. Leading brands like Phantom, Photron, and Vision Research have embraced eco-conscious manufacturing processes, joining the growing ranks of eco-friendly camera gear brands without compromising their renowned performance standards. These innovations include recycled materials in camera bodies, energy-efficient sensors, and modular designs that extend product lifespans.
Today’s high-speed cameras capture stunning footage at up to 1,000,000 frames per second while consuming 40% less power than previous generations. This breakthrough addresses both environmental concerns and practical limitations that historically plagued high-speed photography, such as heat generation and power consumption. Manufacturers have achieved this by developing new CMOS sensors, implementing intelligent power management systems, and utilizing sustainable manufacturing practices.
For professionals and institutions investing in high-speed imaging equipment, these advancements translate to reduced operating costs, extended shooting times, and a significantly lower carbon footprint – all while maintaining the exceptional image quality and precision timing that demanding applications require.
The Environmental Impact of Traditional High-Speed Camera Production
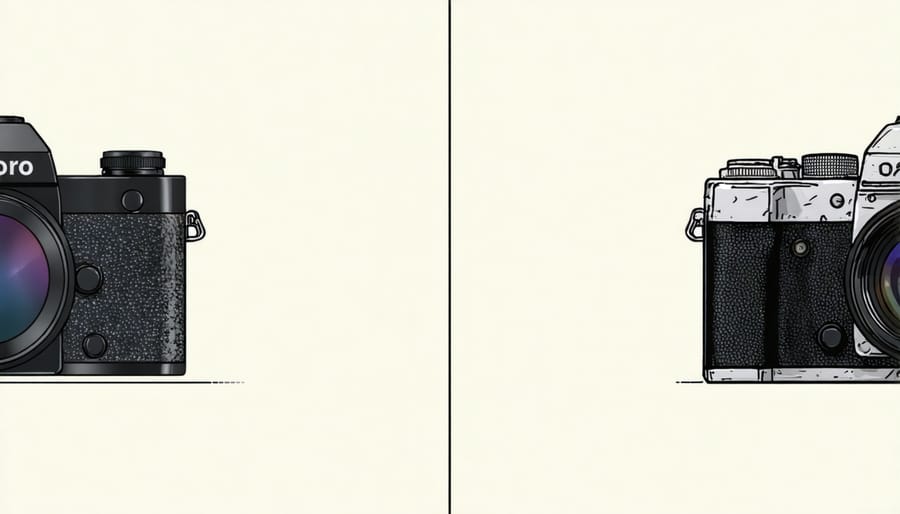
Resource Consumption and Material Waste
High-speed camera manufacturing involves significant resource consumption, particularly in the production of specialized electronic components and precision optical elements. Leading manufacturers like Photron and Vision Research have implemented sophisticated recycling programs for rare earth elements used in sensors and circuit boards, helping reduce their environmental footprint while maintaining product quality.
The production of high-speed camera bodies typically requires aluminum and magnesium alloys, chosen for their durability and heat dissipation properties. Modern manufacturers are increasingly using recycled metals and implementing zero-waste initiatives in their machining processes. For instance, metal shavings from CNC machining are collected, sorted, and repurposed for other industrial applications.
Electronic waste remains a critical concern, especially regarding sensor production and circuit board assembly. However, companies are making strides in sustainable practices by using lead-free solder and implementing take-back programs for end-of-life cameras. Some manufacturers have also started using biodegradable packaging materials and reducing plastic use in accessories.
The industry is gradually moving toward modular designs that allow for easier repairs and component upgrades, extending product lifecycles and reducing overall waste. This approach not only benefits the environment but also provides cost savings for end users.
Energy Usage in Manufacturing
High-speed camera manufacturers face unique challenges when it comes to energy consumption, as their products require significant power to capture thousands of frames per second. A typical high-speed camera system can consume anywhere from 100 to 500 watts during operation, depending on the frame rate and resolution settings.
Leading manufacturers have been implementing various strategies to reduce their carbon footprint. For instance, modern sensor designs now incorporate power-efficient CMOS technology, which consumes up to 70% less energy compared to older CCD sensors. Companies are also developing smart power management systems that automatically switch cameras to standby mode when not actively recording.
In production facilities, manufacturers are increasingly adopting renewable energy sources and energy-efficient manufacturing processes. Some facilities have installed solar panels and LED lighting, while others have implemented heat recovery systems to recycle excess energy from production processes.
These energy-saving initiatives not only benefit the environment but also translate to cost savings for end users. The latest generation of high-speed cameras offers improved battery life and reduced heat generation, making them more practical for extended filming sessions while maintaining their high-performance capabilities.
Leading Sustainable Practices by Major Manufacturers
Recycled Materials Integration
Leading high-speed camera manufacturers are increasingly embracing sustainability by incorporating recycled materials into their products. Companies like Phantom and Photron are pioneering the use of recycled aluminum and plastics in camera housings, while maintaining the rigorous standards required for professional equipment.
These manufacturers have developed innovative processes to repurpose industrial-grade plastics and metals without compromising on durability or heat dissipation properties – crucial factors for high-speed cameras that generate significant heat during operation. For instance, some models now feature camera bodies made from up to 30% recycled materials, with certain components containing even higher percentages.
The integration of recycled materials extends beyond just the external housing. Internal components like circuit board holders, cooling system parts, and non-critical structural elements are increasingly being manufactured using recycled materials. Some manufacturers have even started using recycled glass in their optical systems, though this remains limited to non-critical optical elements.
This shift towards sustainability hasn’t affected camera performance or reliability. In fact, many users report that newer models featuring recycled materials offer improved heat management due to advanced material engineering. Manufacturers are also finding that recycled materials can help reduce production costs, potentially making high-speed cameras more accessible to a broader range of users.
Quality control remains paramount, with manufacturers implementing stringent testing protocols to ensure recycled materials meet or exceed original specifications. This commitment to sustainability while maintaining professional standards represents a significant step forward in eco-friendly imaging technology.
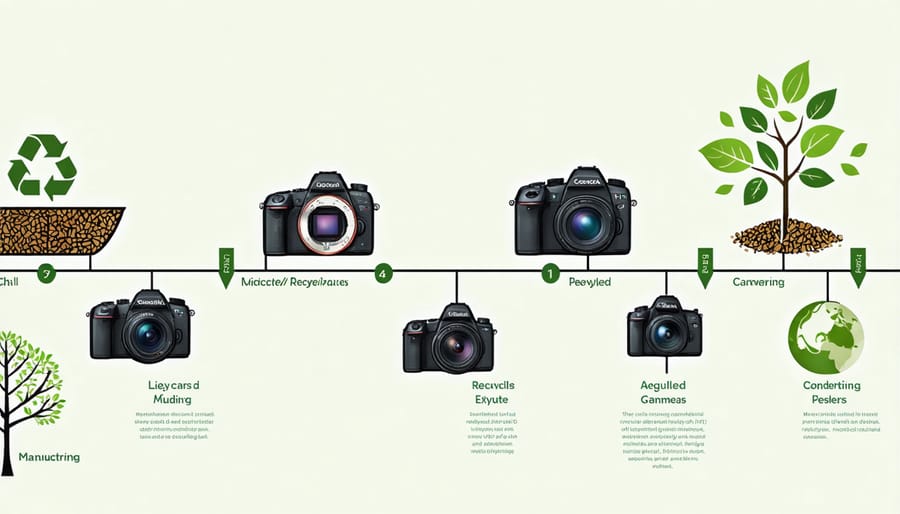
Energy-Efficient Production Lines
Leading high-speed camera manufacturers are increasingly adopting green manufacturing technologies to reduce their environmental footprint while maintaining product excellence. Companies like Phantom and Photron have revolutionized their production lines with smart energy management systems that optimize power consumption during peak manufacturing hours.
These innovations include automated shutdown protocols for equipment during idle periods and the integration of regenerative braking systems in robotic assembly lines, which capture and reuse energy that would otherwise be wasted. Solar panels now power significant portions of many manufacturing facilities, while advanced LED lighting systems with motion sensors ensure minimal energy usage in storage and assembly areas.
Perhaps most impressive is the implementation of heat recovery systems that capture excess warmth from production processes to heat facility spaces and water. This circular approach to energy usage has helped manufacturers reduce their power consumption by up to 40% compared to traditional methods.
Modern facilities also utilize smart scheduling algorithms that coordinate production runs to maximize energy efficiency. By clustering high-energy processes during off-peak hours and implementing advanced insulation techniques, manufacturers have significantly reduced both their carbon footprint and operational costs – savings that often translate to more competitive pricing for end users.
These sustainable practices haven’t compromised product quality; if anything, the precision required for energy-efficient manufacturing has led to even tighter quality control standards.
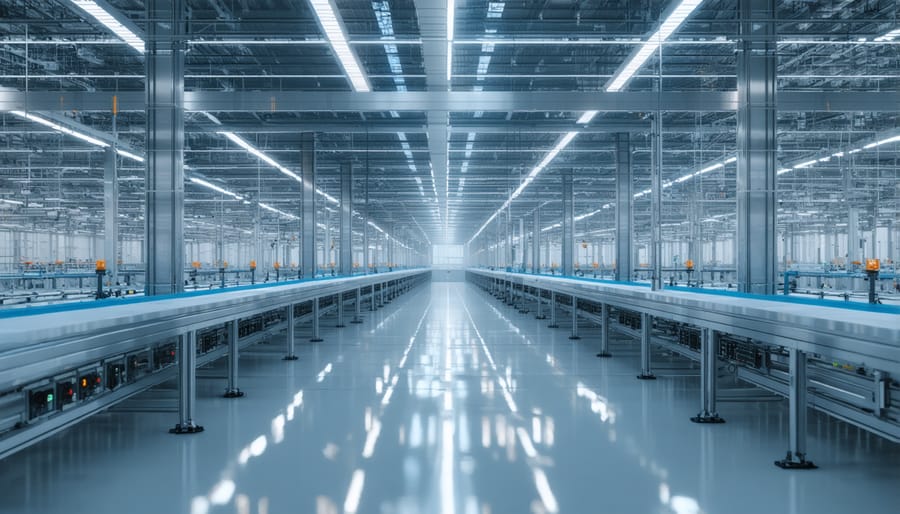
Waste Reduction Strategies
Leading high-speed camera manufacturers are implementing innovative waste reduction strategies throughout their production processes, demonstrating a strong commitment to environmental sustainability. Companies like Phantom and Photron have introduced modular design approaches, allowing for easier repairs and component upgrades rather than complete unit replacement.
Several manufacturers now employ advanced 3D printing techniques for prototyping, significantly reducing material waste compared to traditional manufacturing methods. This approach not only minimizes scrap but also allows for rapid design iterations without generating excess waste materials.
In the packaging department, companies are shifting towards recyclable and biodegradable materials. For instance, Vision Research has replaced traditional foam padding with mushroom-based packaging materials that decompose naturally. Many manufacturers also implement take-back programs, accepting old cameras for proper recycling or refurbishment.
Electronic waste management has become a key focus, with manufacturers implementing strict sorting and recycling protocols for circuit boards, sensors, and other electronic components. Some companies have established partnerships with specialized e-waste recycling facilities to ensure proper handling of sensitive materials.
Water conservation in lens coating and sensor cleaning processes has improved through closed-loop systems that filter and reuse water. Additionally, manufacturers are increasingly adopting lean manufacturing principles, optimizing production workflows to reduce material waste while maintaining the high precision required for these sophisticated imaging devices.
These waste reduction initiatives not only benefit the environment but often result in cost savings that can be passed on to consumers while maintaining product quality.
Future-Forward Sustainability Initiatives
Emerging Green Technologies
In response to growing environmental concerns, high-speed camera manufacturers are making significant strides in developing sustainable manufacturing processes. Leading companies are now implementing zero-waste initiatives and exploring environmentally conscious gear choices throughout their production lines.
One of the most promising developments is the adoption of bio-based materials for camera bodies and components. Several manufacturers are experimenting with recycled polymers and plant-derived plastics that offer the same durability as traditional materials while significantly reducing their carbon footprint. These innovations don’t compromise the cameras’ performance or shock resistance – crucial factors for high-speed photography.
Energy efficiency is another frontier where manufacturers are making remarkable progress. New production facilities are incorporating solar power and smart energy management systems, while newer camera models are being designed with improved battery technology and power-saving features.
Manufacturers are also addressing the end-of-life cycle of their products. Modular designs are becoming more common, allowing for easier repairs and component upgrades rather than complete replacement. Some companies have introduced take-back programs, ensuring proper recycling of old equipment and recovery of valuable materials.
These green initiatives are reshaping the industry while maintaining the high standards photographers expect. As these technologies mature, we’re likely to see more sustainable options become standard features rather than premium additions.
Industry Commitments and Goals
Leading high-speed camera manufacturers are increasingly embracing sustainable practices and setting ambitious environmental goals. Companies like Vision Research, Photron, and NAC Image Technology have pledged to achieve carbon neutrality in their manufacturing processes by 2030. These commitments extend beyond mere carbon reduction, encompassing the entire product lifecycle.
For instance, Phantom cameras, known for their cutting-edge technology, has committed to using 100% recycled materials in their packaging by 2025. They’re also working towards implementing a comprehensive take-back program for end-of-life cameras, ensuring proper recycling of electronic components.
Several manufacturers have joined the Sustainable Imaging Alliance, pledging to reduce energy consumption in their production facilities by 40% before 2028. This initiative includes transitioning to renewable energy sources and implementing smart factory systems that optimize resource usage.
Japanese manufacturer Shimadzu has set a particularly ambitious timeline, aiming to achieve zero-waste manufacturing by 2027. They’re investing heavily in developing bio-based materials for camera components and implementing water conservation measures in their cooling systems.
These industry commitments aren’t just about environmental responsibility – they’re reshaping product development. Manufacturers are increasingly focusing on creating cameras with longer lifespans, modular designs for easier repairs, and components that can be more efficiently recycled. This approach not only benefits the environment but also provides better value to end users through more durable, future-proof equipment.
Consumer Impact and Choices
Performance vs. Sustainability
The intersection of performance and sustainability presents a unique challenge for high-speed camera manufacturers. While consumers demand ever-increasing frame rates and resolution, the energy consumption and materials required to achieve these specifications can have significant environmental impacts.
Many manufacturers are now adopting eco-friendly practices without compromising camera performance. For instance, companies like Vision Research and Photron have implemented energy-efficient cooling systems that maintain optimal sensor temperatures while reducing power consumption by up to 30%. These innovations actually contribute to better image quality by providing more stable operating conditions.
Materials selection has also evolved, with manufacturers using recycled aluminum for camera bodies and biodegradable packaging. Some companies have successfully replaced traditional toxic flame retardants with environmentally friendly alternatives, maintaining safety standards while reducing environmental impact.
However, there are trade-offs. The use of sustainable materials can sometimes add weight to camera bodies, and eco-friendly manufacturing processes may result in slightly higher production costs. Despite these challenges, manufacturers have found creative solutions, such as implementing modular designs that allow for easier repairs and upgrades, extending product lifespan while reducing electronic waste.
The industry is proving that sustainability and performance aren’t mutually exclusive. Recent models demonstrate that cameras manufactured with environmental consciousness can match or exceed the specifications of their conventional counterparts, offering photographers powerful tools while supporting ecological responsibility.
Making Informed Purchasing Decisions
When investing in a high-speed camera, making an informed decision goes beyond just comparing specs and prices. Today’s photographers increasingly consider sustainable photography practices as part of their purchasing criteria.
Start by researching manufacturers’ environmental certifications and commitments. Look for companies that demonstrate transparency about their production processes and materials sourcing. Many leading manufacturers now use recycled materials in their packaging and have implemented energy-efficient manufacturing processes.
Consider the camera’s longevity and repairability. Some manufacturers design their cameras with modular components that can be easily replaced or upgraded, reducing electronic waste. Check if the manufacturer offers repair services and maintains a steady supply of spare parts – this indicates their commitment to product sustainability.
Pay attention to power efficiency ratings and battery technology. Modern high-speed cameras with advanced power management systems not only perform better but also have a smaller environmental footprint. Some manufacturers now use biodegradable materials for non-essential components and offer trade-in programs for older models.
Don’t forget to evaluate the manufacturer’s warranty and support services. A company that stands behind its products with comprehensive warranty coverage often produces more reliable and sustainable cameras. Look for manufacturers who provide firmware updates and software support to extend the camera’s useful life.
Remember, choosing a sustainably manufactured high-speed camera doesn’t mean compromising on quality – many eco-conscious manufacturers are industry leaders in innovation and performance.
As the photography industry evolves, sustainable manufacturing practices in high-speed camera production have become increasingly crucial. Leading manufacturers are not only pushing the boundaries of frame rates and image quality but are also committed to reducing their environmental footprint. Through the adoption of recyclable materials, energy-efficient production processes, and responsible waste management, these companies are setting new standards for eco-conscious manufacturing without compromising product performance.
The shift towards sustainability isn’t just good for the planet – it’s resonating with photographers who want their gear choices to reflect their environmental values. As we look to the future, the success of high-speed camera manufacturers will increasingly depend on their ability to balance cutting-edge technology with sustainable practices. This emerging focus on green manufacturing promises a brighter, more sustainable future for high-speed photography while ensuring that the next generation of cameras continues to meet the evolving needs of professional photographers and enthusiasts alike.